Inventory is a valuable asset that must be managed appropriately. But what is inventory? Learn more about this fundamental aspect of logistics.
Many think of inventory as nothing more than goods stored in a warehouse or items stocked on store shelves. But inventory is more than that; it’s the lifeblood of any logistics operation, and proper inventory management is crucial to success.
This guide defines inventory and explains best practices to reduce costs, boost profit margins, and optimize operations.
What is Inventory?
Inventory refers to a business’s currently held supply of raw materials and finished goods. There are two primary categories of inventory:
- Supply inventory: Raw materials, equipment, and other items used in operations (e.g., spare parts for repairing manufacturing machinery)
- Stock inventory: Finished goods available for purchase
Businesses use inventory to turn a profit. Manufacturers spend money on raw materials, labor, and equipment, which they use to make finished goods. They earn revenue by selling these goods to retailers or directly to consumers. After subtracting costs, they are left with a profit.
Why is Inventory Management Important?
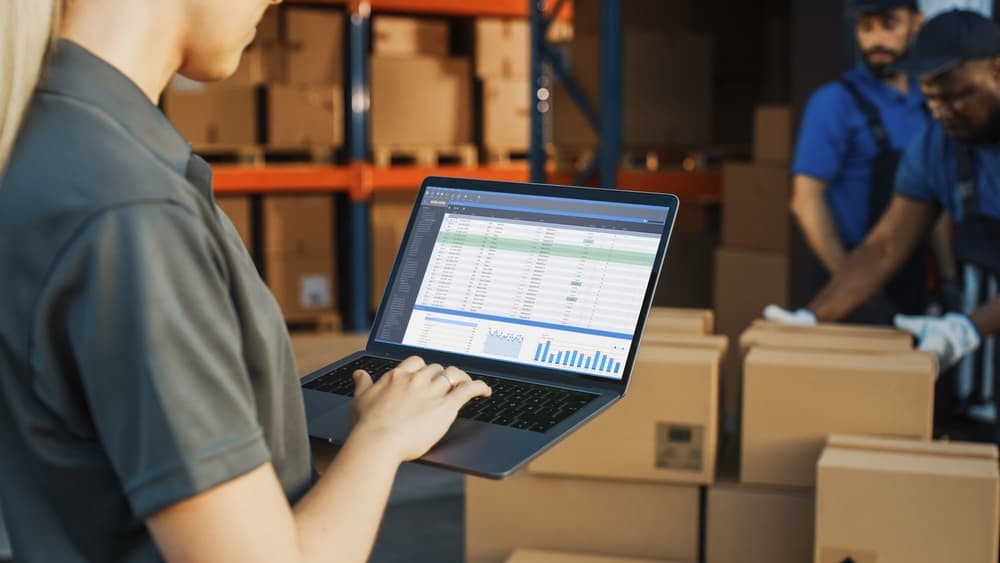
Efficient inventory management is critical for a profitable business. Too little inventory, and you’ll run out and have to put items on backorder. Too much, and you end up with dead stock.
Inventory management also informs resource allocation decisions. When you carefully track inventory levels, estimating how much to spend on raw materials or how many employees a production goal requires is easier.
Tracking Inventory
There's more than one way to count inventory, but the method matters less than knowing how to consistently track, analyze, and manage your raw materials and finished goods. You need to know where your inventory is, where it's going, and how much it's worth. This information helps you make better decisions.
Inventory in Different Industries
What qualifies as inventory depends on your industry. For example, manufacturers count raw materials and semi-finished goods as inventory. Conversely, service-based businesses don't manufacture items for sale, but they do have valuable items they use to turn a profit, such as vacant rooms at a hotel or empty tables at a restaurant.
8 types of Inventory
A company's inventory can take many forms, depending on the industry and the business’s place in the supply chain. Here are eight common types of inventory, plus examples of where they’re found:
1. Raw Materials
Raw materials are the items used to produce finished goods. During production, raw materials are typically transformed into something completely new. For example, a clothing company may cut and sew textiles together and dye them to make clothing.
2. Components
Components are used to create finished goods, but they're different from raw materials. When you use a component, you don't transform it into something completely different; it maintains its original form. Screws and bolts are typical examples of components.
3. Work-in-Progress (WIP)
WIP inventory covers items that are already in production. If a seamstress cuts enough fabric for two shirts and then puts them aside to work on something else, the half-finished shirts become part of the company's WIP inventory.
4. Finished Goods
These are products that have gone through every step of the production process. They’re ready for sale but haven’t been sold to a customer yet. For example, a smartphone is a finished product, as all the components have been assembled into a functioning electronic device. Some refer to finished goods as "stock" inventory to distinguish them from other types.
5. Packing Materials
Packing materials are the items you use to pack your products. They include shrink wrap, boxes, and UPC labels. For example, if your company sells porcelain figurines, you need enough bubble wrap, foam peanuts, or similar packing materials to protect them from damage during shipping.
6. Maintenance, Repair, and Operations (MRO) Goods
MRO goods include spare parts, tools, and consumable supplies used to produce finished goods. Machine lubricant is a good example. It's not a raw material, but you need it to keep your equipment running smoothly.
7. Safety Stock
Safety stock is extra inventory kept on hand to prevent stockouts caused by sudden changes in demand. When the COVID-19 pandemic began, many companies were caught by surprise as consumers demanded much larger quantities of toilet paper and hand sanitizer. A healthy amount of safety stock prevents supply issues.
8. Transit Inventory
Transit inventory refers to the inventory that's moving from one facility to another. For example, a shoe manufacturer may need to transport a truck full of finished goods to a third-party logistics facility.
Inventory Control and its Importance
Inventory control is a set of processes and techniques for maintaining appropriate stock levels. When you carefully control your inventory, you can reduce storage costs, prevent stockouts, and maximize profits.
If you're new to managing business inventory, here's what you can do to find optimal inventory levels:
- Physically organize your stock: It’s challenging to manage inventory if you don't know what you have on hand. A disorganized warehouse or stockroom increases the likelihood that employees will make counting errors, leading to inaccurate records.
- Invest in an inventory management system: Some companies still count their inventory by hand, but manual counts are time-consuming and prone to errors. Tracking inventory assets is easier with a computerized system, which reduces the risk of stockouts and prevents excess stock from accumulating.
- Safeguard your inventory: Take steps to protect raw materials, finished goods, and other types of inventory against damage and theft. If you're concerned about excess moisture in your warehouse, install a dehumidification system, use industrial fans, or open the windows to increase air circulation. Guard against theft by installing a security system, monitoring transactions closely, and limiting employee and customer access to storage areas.
How to Manage Inventory: Best Practices
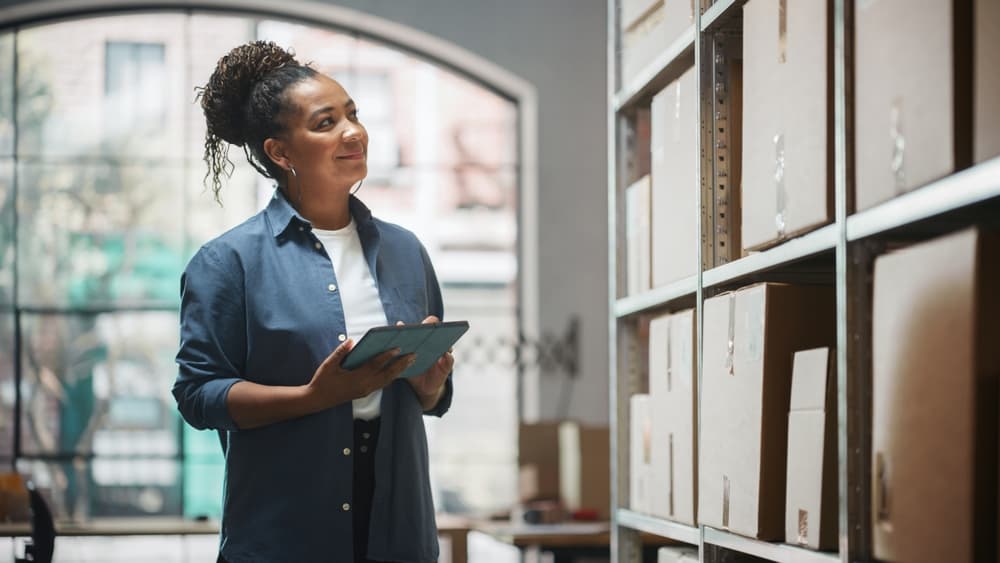
Inventory management is a complex process, but there are straightforward steps you can take to safeguard and streamline your efforts:
Carry Safety Stock
Safety stock lets you stay flexible during sudden changes in market conditions. For example, if a magazine features one of your products on a list of the top gifts for an upcoming holiday, you may see a surge in sales. If stock runs out, you won't be able to fill more orders, leaving customers dissatisfied and limiting your potential revenue.
If you have safety stock on hand, you can fill more of those unexpected orders. Customers will feel better about buying from you, and your company's bottom line will thank you.
Invest in a Cloud-Based Inventory Management Solution
A cloud-based inventory management system helps you track inventory in warehouses, production facilities, and distribution centers. Your team members can access the system from any device with an internet connection. Real-time inventory data enables more informed decisions, preventing stockouts and reducing the likelihood you'll overorder.
Use Batch or Lot Tracking
Batch tracking, also known as lot tracking, lets you track the movement of a specific batch of goods. With a unique lot number, you can do the following:
- Determine which vendors provided the components used to make each item in a batch — helpful if a component turns out to be defective.
- Identify a lot's location.
- Track which customers received products from a specific lot. This information is invaluable if you have to issue a recall.
Inventory FAQs
Inventory may be a fundamental aspect of logistics, but it raises many complicated questions. Here are our answers to some common queries:
What is Inventory Turnover?
Inventory turnover is a ratio measuring how well a company manages its inventory. The ratio divides the cost of goods sold in a given period over the average cost of inventory during that same period, usually one quarter or one year.
A high inventory turnover is desirable because it indicates you sell through stock quickly, implying lower carrying costs. Firms also use inventory turnover to determine how successfully they anticipate customers' needs.
What is Inventory Analysis?
Inventory analysis involves assessing how the demand for different products changes over time. This analysis helps you stock just the right amount of inventory. It also identifies your most profitable products.
Who Provides the Best Inventory Management Examples in Retail?
It's no secret that Walmart is one of the top companies in the world. Walmart achieves its goals with the aid of superb inventory management practices.
The store’s Retail Link system shares data with suppliers, ensuring everyone is on the same page regarding replenishing product inventory in a timely fashion. Walmart also uses automated tools to forecast consumer demand, facilitating response to sudden changes in the retail industry.
Revolutionize Your Inventory Management with Orderful
Every company carries some type of inventory, and managing that inventory is a critical aspect of operations. Efficient inventory management optimizes profits by reducing waste, preventing theft, and ensuring you always know where your products are.
Orderful offers a cloud-based EDI platform so you can exchange electronic documents with your trading partners and stay up to date on your supply chain. Contact us today to speak to an EDI expert about how our modern EDI solution increases efficiency and minimizes errors.