Bottlenecks in business slow operations, reduce throughput, and increase costs. Learn what a bottleneck is, how it affects production systems, and what you can do to fix it.
What Is a Bottleneck in Business?
A bottleneck in business is a point of friction that limits the flow of a process, causing delays, inefficiencies, or added costs. Understanding what a bottleneck is—and how to spot one—can help you fix issues before they impact your bottom line.
Think of it like this: Your team is moving fast, but one step in the process consistently causes slowdowns. That’s your bottleneck. Left unchecked, it becomes a costly drag on your business.
Bottleneck Meaning in Business Operations
A bottleneck refers to any constraint that reduces the capacity of a system. This could be a machine that can’t keep up, a delayed supplier, or a team that’s overloaded.
In operations management, bottlenecks can impact:
- Production timelines
- Labor efficiency
- Inventory turnover
- Customer satisfaction
By identifying bottlenecks early, you can improve output and create more resilient processes.
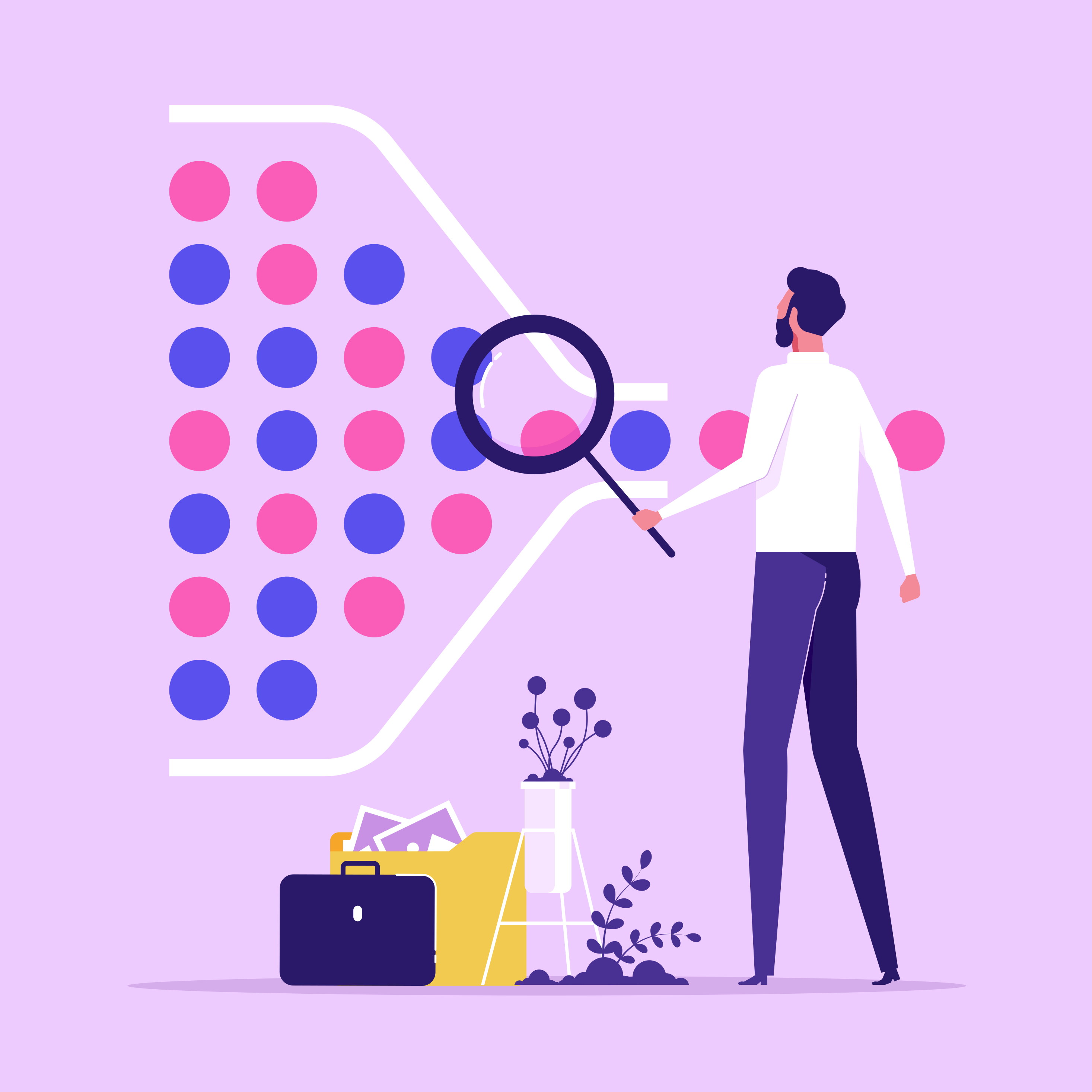
Example of a Bottleneck in Business
Picture a production line where one machine works twice as slowly as the others. As products move down the line, they begin piling up at that slower station. That’s a classic bottleneck operation example—and a prime target for improvement.
Other examples include:
- A key decision-maker approving every invoice
- Delayed materials from overseas suppliers
- Incomplete handoffs between teams using disconnected systems
Each of these can trigger business bottlenecks with cascading effects across your operations.
4 Types of Business Bottlenecks
1. Process Bottlenecks
Caused by inefficient workflows or broken communication. Example: delayed approvals or unclear project roles.
2. Resource Bottlenecks
Caused by missing inputs like inventory or raw materials. Example: running out of chicken in a restaurant due to supplier delays.
3. Capacity Bottlenecks
Caused by a physical or system constraint. Example: a bottling machine can only process 500 bottles/hour, while upstream stations produce 800/hour.
4. People Bottlenecks
Caused by limited decision-making bandwidth. Example: all pricing decisions must go through one manager, causing slow turnaround.
Type | Description | Real-World Example |
---|---|---|
Process | Workflow delays or inefficient communication | Product development delayed by multiple approval layers |
Resource | Missing materials or inputs halt progress | Supplier issues lead to empty shelves at a restaurant |
Capacity | Limited throughput in a step or system | Packaging station can't keep up with production line |
People | Single decision-maker or short-staffed teams | Manager bottlenecks cause team inaction during peak demand |
Bottlenecks and Production Capacity
Theoretical capacity assumes everything works perfectly—no downtime, no delays. But real businesses operate under practical capacity, which accounts for resource limits, equipment wear, and scheduling challenges.
A bottleneck shows up when one part of your process limits that practical capacity. It reduces throughput and increases the cost per unit.
How Bottlenecks Affect Profitability
Consistent slowdowns increase labor and operational costs. That results in production volume variance—the difference between expected vs. actual output costs.
You might see:
- Increased man-hours per unit
- Spoilage or waste due to delays
- Missed delivery timelines
- Lower margin on high-demand SKUs
Solving bottlenecks helps reduce these variances—and protect your profitability.
Why Bottleneck Management Matters
Identifying and eliminating bottlenecks helps your business move faster, smarter, and more sustainably.
Benefits Include:
- Reduced burnout: Smoother workflows mean less overtime and fewer last-minute scrambles.
- Improved customer experience: Reliable timelines build trust and reduce backorders.
- Higher throughput: When the constraint is removed, the whole system speeds up.
- Lower operating costs: You do more with the same people and tools.
4 Strategies to Prevent Bottlenecks in Business
1. Monitor and Forecast Demand
Use historical data and seasonal trends to predict surges and prepare accordingly—especially for businesses with cyclical volume, like food and beverage or CPG.
2. Analyze the Right Metrics
Don’t just focus on the last step where the delay occurred. Use tools like fishbone diagrams to identify the root cause of process slowdowns.
3. Streamline Workflows
Rework overly complex handoffs and approval processes. Invest in real-time visibility tools to improve communication between teams and vendors.
4. Strengthen the Weak Links
Sometimes the fix is simple: hire more staff, buy better equipment, or automate manual steps. Reinforce known constraints to prevent system-wide slowdowns.
Remove Bottlenecks with Modern EDI
Many bottlenecks stem from poor inter-company communication—especially when key data like purchase orders or inventory updates moves slowly.
That’s where Orderful comes in, as demonstrated by Darn Tough's successful use of Orderful.
Our cloud-native EDI platform makes it easy to exchange data across your trading partners in real time. Faster, cleaner communication means fewer errors, faster turnaround, and no more waiting on outdated systems.
Ready to modernize your supply chain and eliminate communication bottlenecks?
Bottleneck in Business FAQ
What is a bottleneck in business?
A bottleneck in business is a step in a workflow or process that slows down the entire system, limiting throughput and reducing efficiency.
What is meant by a bottleneck in operations management?
A bottleneck in operations management is a constraint—such as limited equipment, labor, or input—that reduces a system’s output and creates delays across the production process.
What is a bottleneck in business with an example?
A bottleneck in business is a slowdown caused by a limited resource. For example, if one machine on a production line is slower than the rest, it becomes a bottleneck that holds up the entire operation.
What does bottleneck mean?
Bottleneck means a point of congestion or restriction that delays progress in a system, process, or workflow.
How can you identify business bottlenecks?
You can identify business bottlenecks by tracking where delays occur, monitoring capacity usage, and analyzing process data for recurring slowdowns or resource limitations.
- 01What Is a Bottleneck in Business?
- 02Bottleneck Meaning in Business Operations
- 03Example of a Bottleneck in Business
- 044 Types of Business Bottlenecks
- 05Bottlenecks and Production Capacity
- 06How Bottlenecks Affect Profitability
- 07Why Bottleneck Management Matters
- 084 Strategies to Prevent Bottlenecks in Business
- 09Remove Bottlenecks with Modern EDI
- 10Bottleneck in Business FAQ